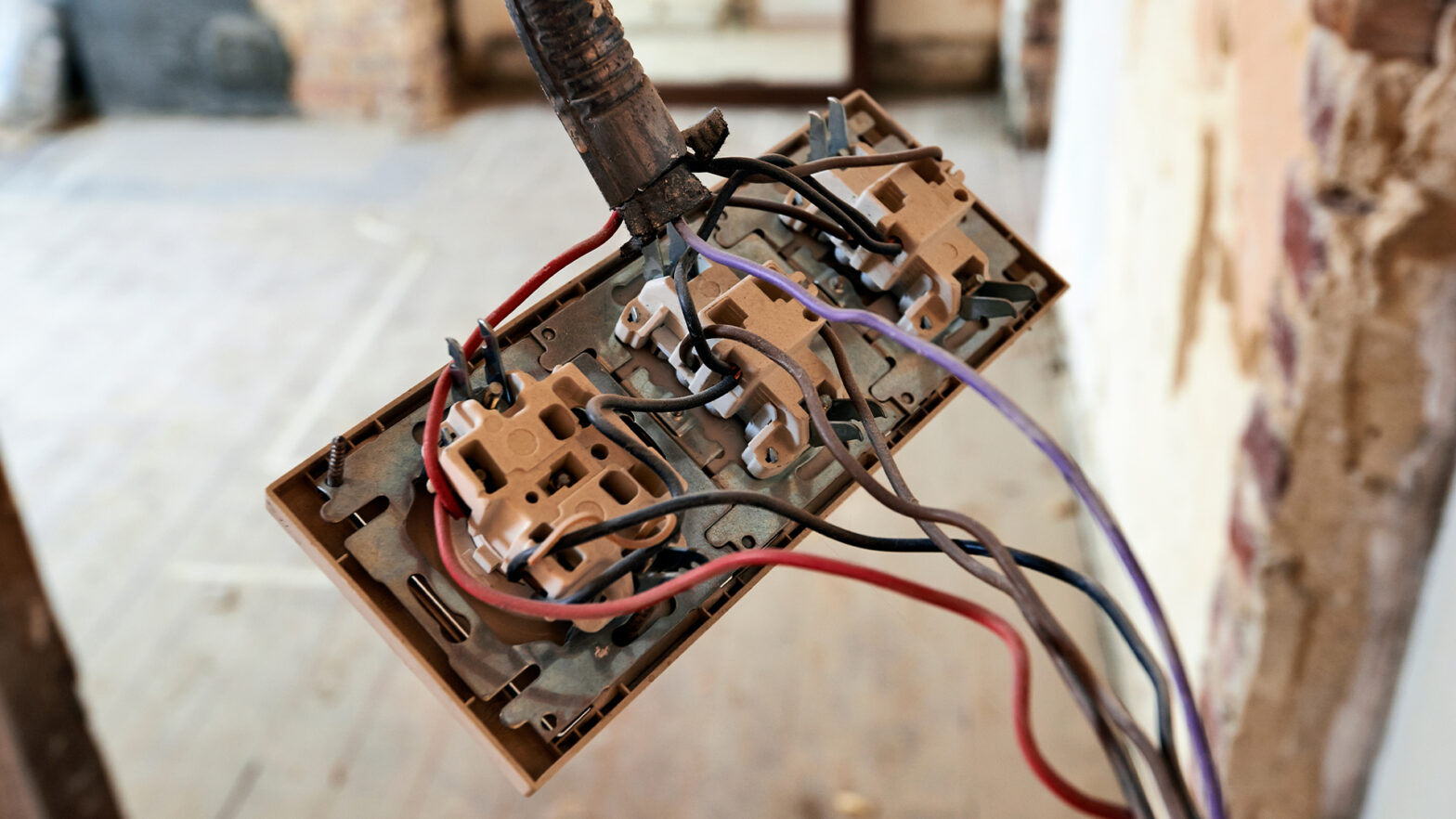
Construction, architecture and engineering professionals face countless threats on a jobsite. From exposed wires to rain, many technological and natural influences could lead to a notable incident. Awareness and prevention are essential for keeping workers safe. Knowing the most common risks is the first step to prevent electrical failure on jobsites.
Insufficient Personal Protective Equipment (PPE)
Contractors could wear damaged or inadequate PPE. They may also be unable to recognise when the garment is incorrect for the project or has a harmful compromise. Preventing PPE failures happens through education.
The workforce should know what is required for each role, including nonconductive hard hats, insulated gloves, ear plugs, safety glasses and safe footwear. Companies should demand staff wear flame-resistant clothing, as electrical work could spark an arc flash at any moment. Teams must know how to appropriately don and doff attire to prevent damage, while inspecting each item before and after use for issues.
Companies and technicians should also be familiar with the compliance frameworks dictating PPE. ANSI and OSHA are the most important.
Working Near Overhead Power Lines
Whether deep in scaffolding or operating a crane, construction workers and engineers could accidentally knock against an overhead power line. It could cause electrocution or burns with immediate contact, or worse, if it falls to the ground and impacts other employees.
Thorough surveys of the jobsite before breaking ground will give everyone greater visibility. The maps should include height measurements and coordinates of each power line. Convey to teams the closest distance they can approach before causing safety concerns, especially with electrical equipment in tow. Clearance requirements may vary based on the circumstances.
Other simple behavioural changes, like looking up before moving or commanding equipment, will prevent electrical failure on jobsites.
Lack of Lockout/Tagout (LOTO) Procedures
Maintenance should prevent safety incidents, but if contractors do not power down equipment fully beforehand, repairs could become a dangerous assignment. Firms must relay to all staff how to abide by the regulatory requirements for LOTO. Everyone should know the consequences of leaving equipment energised and untagged because it could lead to some of the most severe accidents.
Damaged Tools, Equipment and Electrical Parts
Exposed and damaged tools and wires lead to shocks, burns, fires and other safety hazards. Open power distribution units, poorly insulated cords and temporary electrical fixtures, like lights on the jobsite, all pose similar dangers. Workers should know how to identify faults simply by looking at the equipment. No manual intervention should be necessary, as this could lead to an injury.
Inefficient tool use would also fall under this category, as tons of machinery degrade over time with improper usage. They could lead to additional safety and environmental concerns. For example, electrical problems in compressors release 40% more carbon emissions from excess energy use. The fossil fuels lead to air pollution and health problems for workers. Concerns like this show how diverse adverse electrical impacts can be.
Staff should also know how to report or repair damaged equipment. Following LOTO protocols beforehand is crucial for eliminating the most severe accidents.
Improper Grounding
Contractors risk electrocution if there is no safe path for the energy to go. Plugs should have an ever-present grounding pin. The site should know the importance of these fixtures and learn how to spot sockets and plugs with insufficient prongs. Sites can also use other tools, like ground-fault circuit interrupters (GFCIs) as a backup measure.
Wet Conditions
Light drizzling and small puddles are as severe as massive rainstorms on a site, even if not working directly with electrical equipment. Companies should not let technicians work in wet conditions. If an unexpected storm occurs, the staff should know how to protect themselves and the equipment from damage. Machines should already have watertight storage units or corrosion-resistant materials to mitigate the water’s impacts.
A little moisture can cause the most experienced professionals to lose grip or control of tools they have used for years. Around 107,000 safety incidents occur with manual tools yearly, including hammers and screwdrivers. The number is higher when considering powered equipment, but wet conditions impact every aspect of the jobsite. Contractors must do their due diligence by inspecting tools exposed to the rain before powering them up again.
Overloading Circuits
If too many devices are on a single circuit, especially a temporary power supply for machinery, the system may be unable to handle the surge. Circuit breakers and GFCIs are invaluable for distributing power and ensuring each source can handle load burdens. Extension cords are also easy-to-access tools for transmitting energy more safely, though they could cause tripping and falling incidents if not placed strategically.
One-Line Diagrams
One-line diagrams show workers a building or worksite’s energetic flow. They are vital for mapping what systems and transmission technologies impact one another. People drafting them should use the standardised symbols and procedures.
Contractors can see how their section of the project can impact even the most distant parts of the site. Field inspectors should brief workers on these documents before sending them to work and keep them in accessible locations as helpful reminders.
Prevent Electrical Failure on Jobsites With Education
Training and awareness are the best ways to combat common construction and engineering oversight. While implementing technology and other strategies are ideal supplementary solutions, consistency only occurs as safety knowledge in the staff base deepens. Mending gaps in understanding about the variety and severity of electrical failures makes the protocols mean more to each worker, ensuring long-term sustainability of safety education.